Leaks and failures of operating reactors in chemical and other industries results in significant economical losses and risk plant personnel. Periodic inspections performed by ultrasonic, magnetic particles, liquid penetrant and other non-destructive test (NDT) methods require costly shutdowns, insulation removal and cleaning. In many cases periodic NDT cannot be performed with optimal time intervals. Due to these and other limitations, acoustic emission (AE) technology can provide an excellent addition to the complex of measures used to increase operational safety of reactors and reduce probability of failure.
Acoustic emission technology is based on detection and analysis of acoustic emission (stress) waves radiated during elementary crack propagation, local plastic deformation development around stress concentrators such as inclusions or other. Once emitted, acoustic emission waves propagate along the inspected structure for distances of meters and then are detected by special acoustic emission sensors that convert mechanical disturbance produced by AE waves into electrical signals.
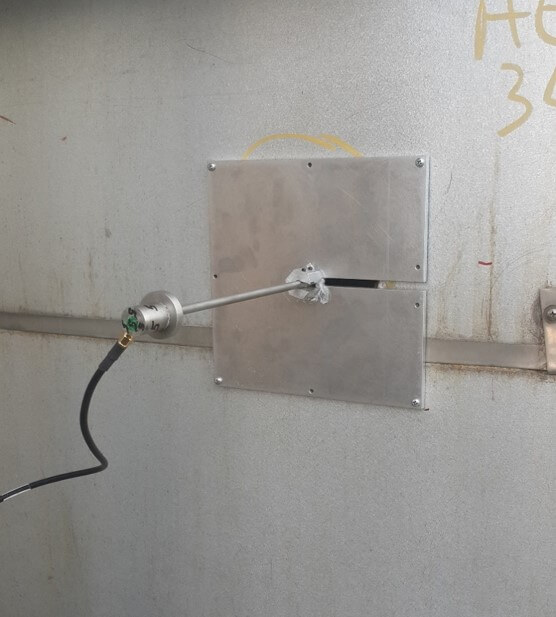
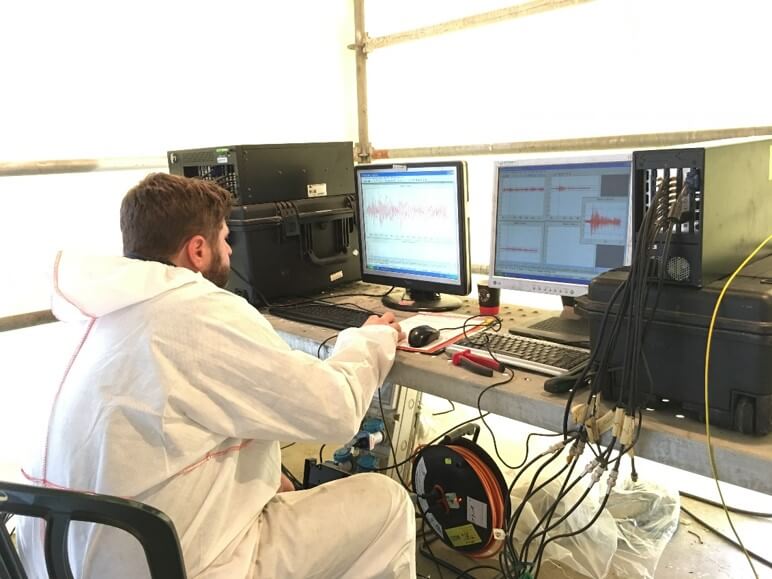
Figure 2. Acoustic Emission monitoirng in process.
Special analysis of detected AE signals is then performed to locate acoustic emission flaw sources, identify flaw type, evaluate rate of flaw propagation and it sensitivity to load/stress/operational changes. Other mechanical sources of Acoustic Emission (AE) are friction and impacts, detection and analysis of which are used to identify leaks, friction, vibrations and others.
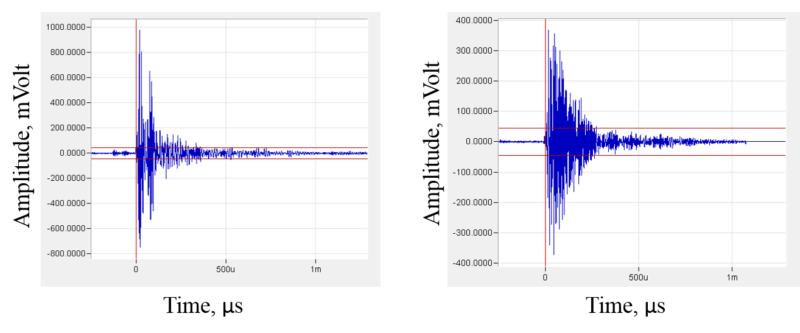
Important advantages and addition of acoustic emission to other non-destructive testing are:
- Proven detection of micro and macro-scopic cracks due to fatigue, stress corrosion, creep and other failure mechanisms.
- Detection of plastic deformation development of metals and buckling.
- Ability to monitor flaw development continuously without interruption of operational conditions.
- Acoustic emission testing can be applied to reactor operating at 600 deg C or even higher temperatures.
- Detect flaws without significant limitations related to their position in a reactor, without insulation removal and without interference with reactor operation.
- Prolong operational time.
- Guide other NDT to areas with flaw indications.
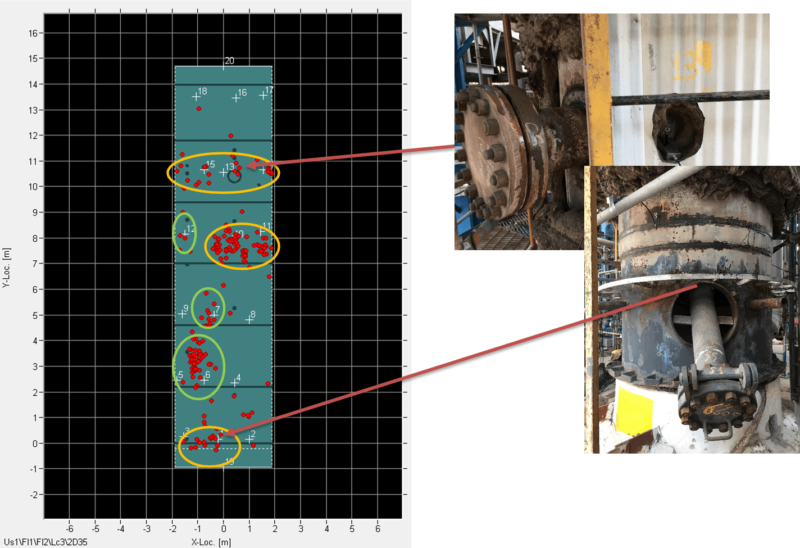
Figure 4. Location of AE sources in a reactor.
Acoustic emission in-service inspection comply with several international standards including:
- ASTM E1139: Standard Practice for Continuous Monitoring of Acoustic Emission from Metal Pressure Boundaries.
- ASME Standard: Section V, Article 13, Boiler & Pressure Vessel Code, Continuous Acoustic Emission Monitoring.
- ASTM E1211: Standard Practice for Leak Detection and Location Using Surface-Mounted Acoustic Emission Sensors.
- ASTM E569: Standard Practice for Acoustic Emission Monitoring of Structures during Controlled Stimulation.
For more about in service inspection of reactors and other equipment please visit: www.idinspections.com or by email: bm@idinspections.com
#AcousticEmission #SturcturalHealthMonitoring #NDT #Reactors